The pursuit of excellence is an endless journey. Every improvement, no matter how small, paves the way for superior performance. Discover how the Kaizen method can transform your organization.
🔥 Nous recommandons Ideamap
Ideamap est l’outil idéal pour un brainstorming ou un projet collaboratif. Grâce son interface facile et à ses fonctions IA, Ideamap booste votre créativité tout en favorisant une meilleure organisation de vos idées pour atteindre vos objectifs.
The Kaizen method, originating from Japan, has become an essential pillar for companies seeking to optimize their processes and promote a culture of continuous improvement. By adopting this approach, organizations can not only increase their efficiency but also engage their employees in a positive and proactive dynamic. This article explores in depth the definition, principles, and implementation of the Kaizen method, offering valuable insights for any enterprise aspiring to excellence.
Definition of the Kaizen Method
The Kaizen method is a philosophy of Japanese origin that literally translates to “change for the better.” It focuses on the continuous improvement of processes, products, and services within an organization. Unlike approaches that aim for major and isolated reforms, Kaizen prioritizes small, regular improvements involving all collaborators, from operational staff to management.
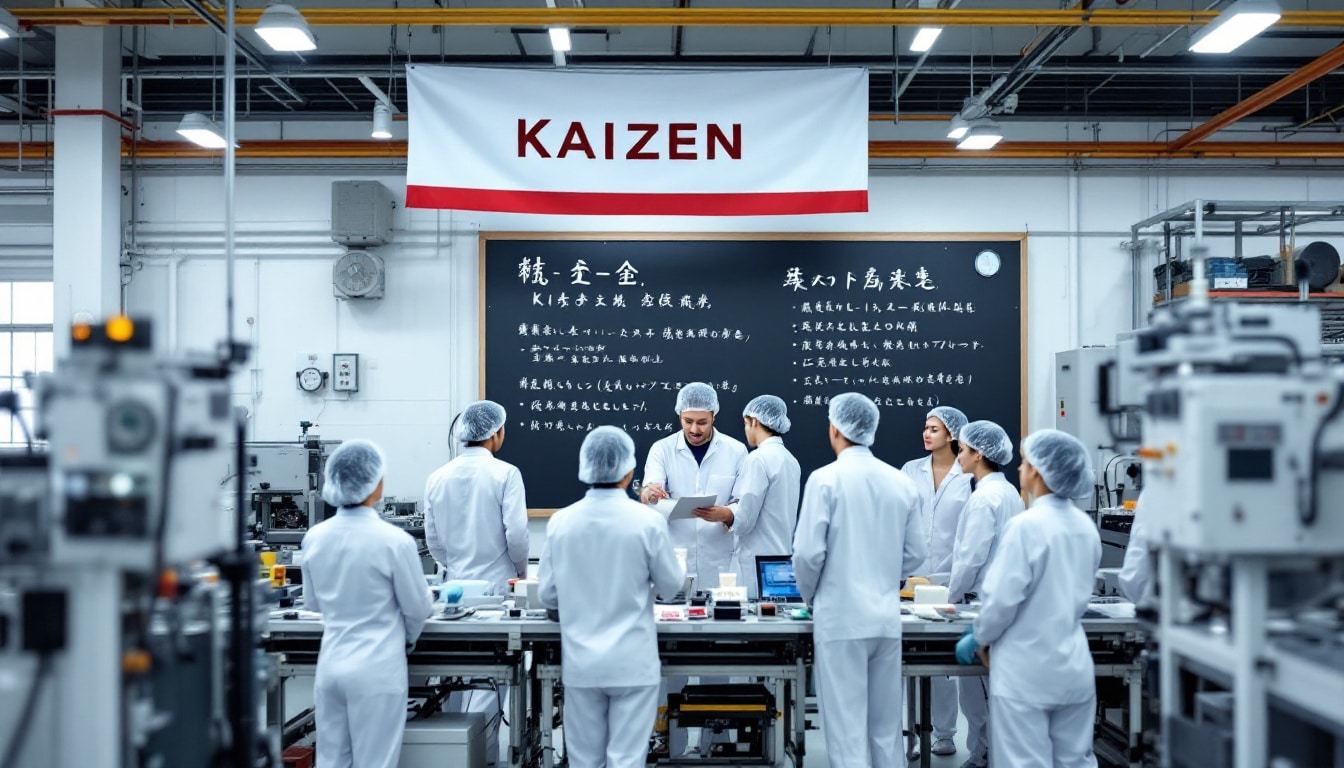
Introduced by Masaaki Imai in the 1980s, the Kaizen method was quickly adopted by industrial giants such as Toyota, Honda, and Samsung, who recognized its benefits in terms of productivity and quality. This approach fits within the broader framework of Lean Management, aiming to eliminate waste and optimize resources.
The heart of Kaizen lies in the active participation of all levels of the organization. Every employee is encouraged to identify opportunities for improvement and propose innovative solutions. This culture of collaboration not only strengthens team engagement but also fosters essential adaptability in the face of market challenges.
In 2025, the application of Kaizen extended beyond traditional industrial sectors, impacting areas such as healthcare, education, and financial services. Companies like Sony and Mitsubishi have integrated Kaizen into their management strategies, thus demonstrating its flexibility and effectiveness in various organizational contexts.
The successful implementation of Kaizen relies on a clear understanding of its fundamental principles and on the continuous commitment of the entire team. By adopting this method, businesses can not only improve their operational performance but also create a stimulating and motivating work environment.
Fundamental Principles of Kaizen
The Kaizen method is structured around several key principles that guide its application and ensure its effectiveness. These principles are designed to foster a culture of continuous improvement and shared responsibility within the organization.
Continuous Improvement
At the core of Kaizen is the idea of continuous improvement. Rather than aiming for radical changes, this approach prioritizes small regular modifications that accumulate to generate significant long-term improvements. This method allows for a flexible and gradual adaptation to market changes and customer needs.
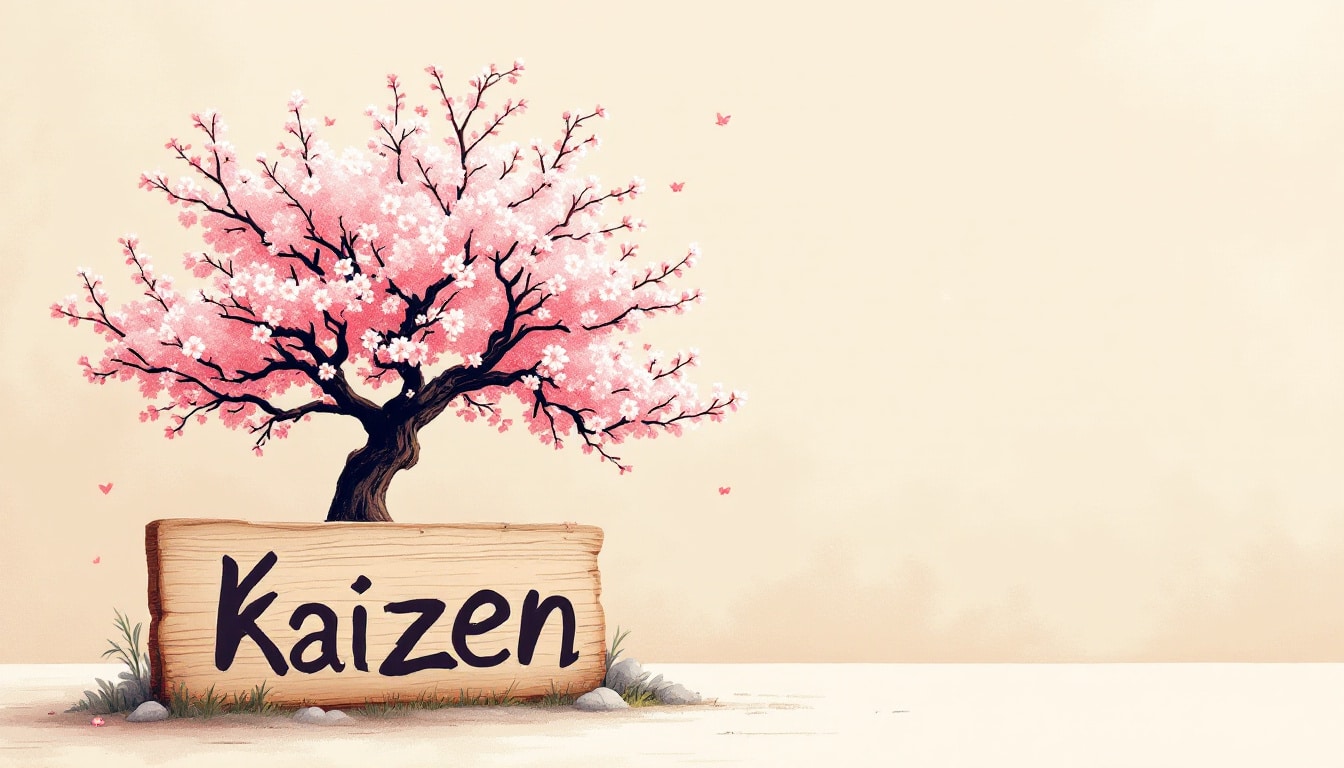
Elimination of Waste
Another fundamental principle is the elimination of waste, or Muda. This involves identifying and removing all activities that do not add value to the final product or service. At the same time, Kaizen also addresses Mura (inconsistency) and Muri (overburden), thereby aiming for a comprehensive optimization of processes.
Companies like Panasonic and Toshiba have demonstrated the effectiveness of this principle by reducing unnecessary costs and improving the quality of their products. The elimination of waste not only reduces costs but also enhances customer satisfaction by offering higher quality products and services.
Participation of All
Kaizen relies on the active participation of all employees, regardless of their hierarchical level. This bottom-up approach encourages every team member to contribute to process improvement, thereby fostering a sense of belonging and shared responsibility.
At Nissan and Canon, this philosophy has been integrated into daily practices, with each employee trained to identify opportunities for improvement and propose solutions. This involvement strengthens team cohesion and stimulates innovation within the company.
Standardization of Processes
The standardization of processes is essential to ensure the consistency and quality of the improvements made. By defining clear and uniform procedures, companies can guarantee an effective implementation and repeatability of the successes achieved through Kaizen.
The 5S system, which includes Sort, Set in Order, Shine, Standardize, and Sustain, is often used to organize and optimize the work environment. This method, adopted by leaders like Hitachi and Honda, helps create orderly and effective workspaces, thereby facilitating the detection and resolution of problems.
Use of the PDCA Cycle
The Plan-Do-Check-Act (PDCA) cycle is another essential component of Kaizen. This iterative cycle allows for planning an improvement, implementing it, checking its results, and acting accordingly. This method promotes a systematic and thoughtful approach to continuous improvement.
By applying the PDCA cycle, companies can test new ideas in a controlled manner, evaluate their impact, and adjust their actions to maximize benefits. This approach encourages experimentation and adaptability, which are key elements for maintaining sustainable competitiveness.
In summary, the principles of Kaizen provide a solid framework for establishing a culture of continuous improvement, essential for the growth and sustainability of businesses in a constantly evolving economic environment.
Implementing Kaizen in the Workplace
Implementing the Kaizen method requires a structured approach and total involvement from all employees. Here are the key steps to effectively integrate Kaizen into your organization.
Management Commitment
The success of Kaizen starts with a firm commitment from management. Leaders must not only understand the principles of Kaizen but also embody them daily. This visible commitment inspires employees and encourages them to actively participate in the improvement process.
At Mitsubishi and Panasonic, leaders play a central role in promoting Kaizen by allocating resources, recognizing team efforts, and creating an environment conducive to innovation.
Training and Awareness
For Kaizen to be effective, it is crucial to train employees in the tools and techniques of this method. Workshops, seminars, and ongoing training help develop the necessary skills and raise staff awareness about the importance of continuous improvement.
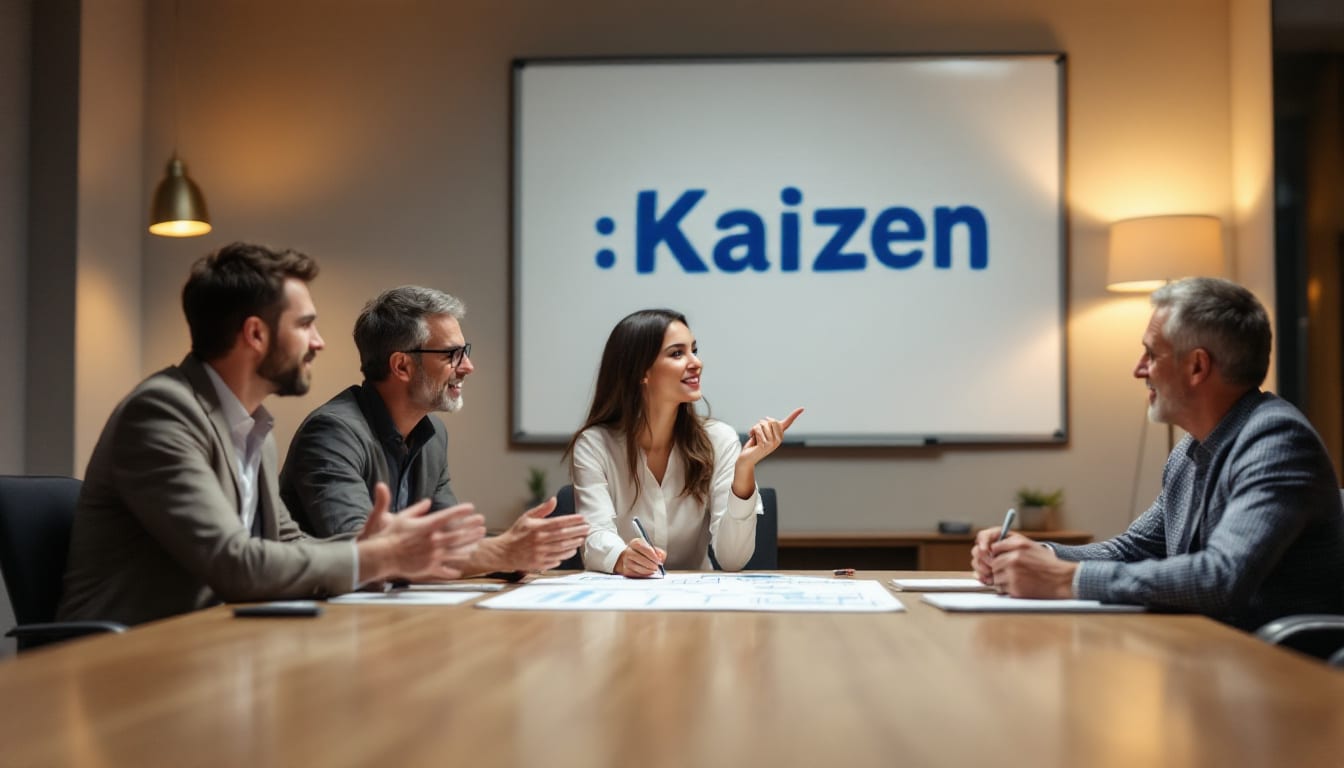
Companies like Sony and Canon invest in the training of their teams, thus ensuring a shared understanding of the objectives and methods of Kaizen. This training fosters adherence and active participation from all members of the organization.
Identifying Improvement Opportunities
Once employees are trained, the next step is to identify areas that can be improved. This can be done through direct observations, regular feedback, or brainstorming sessions. The goal is to detect inefficiencies and wastes that hinder the company’s performance.
For example, Toyota uses tools such as Gemba Walks to observe processes in real time and gather valuable insights on the ground. This approach helps understand the challenges faced by employees and find suitable and pragmatic solutions.
Developing and Testing Solutions
Once improvement opportunities have been identified, it is crucial to develop concrete solutions and test them iteratively. The PDCA cycle (Plan-Do-Check-Act) is particularly useful in this phase, allowing for controlled implementation of changes and evaluation of results before generalizing them.
Kaizen Events are intensive work sessions where multidisciplinary teams focus on a specific problem for a set period of time. This approach fosters collaboration and innovation, allowing for the rapid generation of significant improvements.
Monitoring and Evaluating Results
After implementing the solutions, it is essential to monitor and evaluate their results. This allows measuring the impact of the changes and identifying necessary adjustments to maximize benefits. Tools such as real-time Dashboards offer complete visibility on performance and facilitate informed decision-making.
Companies like Hitachi use interactive dashboards to track key performance indicators (KPI) and ensure proactive management of improvements. This transparency helps maintain a positive dynamic and guarantees that improvement efforts continue to yield tangible results.
Strengthening the Culture of Continuous Improvement
To sustain the benefits of Kaizen, it is essential to reinforce a culture of continuous improvement within the organization. This involves recognizing individual and collective efforts, celebrating successes, and encouraging constant innovation.
By adopting an inclusive and participative approach, companies can ensure that Kaizen becomes second nature, integrated into all facets of activity. This culture not only promotes operational efficiency but also creates a fulfilling and motivating work environment.
To learn more about the implementation of Kaizen, consult this detailed article.
Use Cases: Toyota, Sony, and Other Leaders
The successes of companies like Toyota and Sony perfectly illustrate the advantages of the Kaizen method. By integrating this philosophy, these leaders have been able to maintain their dominant position in the market through continuous improvement of their processes and products.
Toyota: The Pioneer of Kaizen
The production system of Toyota is often cited as the flagship example of the successful application of Kaizen. By focusing on the elimination of waste and the optimization of processes, Toyota has been able to reduce costs, improve quality, and increase customer satisfaction. Regular Gemba Walks enable managers to directly observe operations and identify potential improvements, fostering a culture of responsiveness and adaptability.
Sony: Continuous Innovation
At Sony, Kaizen manifests itself in an incessant quest for innovation and quality. By encouraging employees to propose improvement ideas, Sony has been able to develop cutting-edge products that meet the changing demands of consumers. This approach has also strengthened the company’s competitiveness in highly dynamic markets.
Other Success Stories
Other companies such as Honda, Canon, and Panasonic have also successfully adopted Kaizen. Each organization adapts the principles of Kaizen to its specificities, but all share a common desire for continuous improvement and commitment from their teams. These companies demonstrate that Kaizen is a flexible method capable of adapting to different sectors and operational contexts.
In 2025, the principles of Kaizen continue to influence new industries, including cutting-edge technologies and digital services. This widespread adoption illustrates the relevance and lasting effectiveness of Kaizen in a constantly evolving economic environment.
To discover more cases of Kaizen application, consult this article.
Tools and Techniques for Applying Kaizen
The success of the Kaizen method relies on the effective use of various tools and techniques that facilitate the identification and implementation of improvements. Here are some of the most commonly used tools within the Kaizen framework.
The 5S System
The 5S system is a workplace organization methodology aimed at improving efficiency and reducing waste. The five steps are: Sort (Seiri), Set in Order (Seiton), Shine (Seiso), Standardize (Seiketsu), and Sustain (Shitsuke). By applying these principles, companies can create a more orderly, safe, and productive work environment.
Companies like Mitsubishi and Hitachi have integrated 5S into their daily practices, witnessing a significant reduction in errors and improved product quality.
Gemba Walks
Gemba Walks involve managers going directly to the workplace (the “Gemba”) to observe ongoing processes, engage in discussions with employees, and identify opportunities for improvement. This practice fosters a deep understanding of operations and enables proactive problem-solving.
At Toyota, Gemba Walks are an essential component of daily management, allowing for direct communication and increased responsiveness to operational challenges.
The PDCA Cycle
As previously mentioned, the Plan-Do-Check-Act (PDCA) cycle is a fundamental tool of Kaizen. It structures improvement efforts into clear steps: plan a change, implement it, check its effects, and adjust actions accordingly. This iterative cycle ensures continuous improvement and constant adaptation to new requirements.
By utilizing PDCA, companies can methodically test new ideas and minimize the risks associated with changes while maximizing the chances of success.
Kaizen Events
Kaizen Events are intensive workshops aimed at solving specific problems or improving particular processes within a limited timeframe. These events mobilize multidisciplinary teams to collaborate in a focused manner, thus generating innovative and pragmatic solutions.
For example, Canon regularly organizes Kaizen Events to optimize its production lines, thereby improving quality and reducing manufacturing lead times.
Kanban and Dashboards
Kanban is a visual tool that allows tracking the progress of tasks and projects in real-time. By using boards with columns such as “To do,” “In progress,” and “Done,” teams can visualize the workflow and quickly identify bottlenecks.
Software like ProjectManager offers advanced features for creating and managing digital kanban boards, thereby facilitating collaboration and tracking improvement projects.
By integrating these tools and techniques, companies can effectively structure their improvement efforts, ensuring a successful implementation of Kaizen and continuous optimization of their operations.
Measurable Benefits of Kaizen
Adopting the Kaizen method brings tangible and measurable benefits to the organizations that implement it. These benefits extend beyond process improvement, impacting the culture and overall performance of the business.
Increased Productivity
By eliminating waste and optimizing processes, Kaizen enables a noticeable increase in productivity. Companies can achieve more with the same resources, thereby improving their profitability and competitiveness in the market.
For example, Honda has observed a significant reduction in production times due to the rigorous application of Kaizen principles, thereby increasing its production capacity without massive investments.
Quality Improvement
Kaizen places a strong emphasis on quality, ensuring that each step of the process contributes to a high-quality product or service. This attention to detail helps reduce defects, improve customer satisfaction, and enhance the company’s reputation.
Sony, for instance, uses regular audits and continuous feedback to maintain high-quality standards, thus ensuring customer loyalty and its position as an innovative leader in the technology industry.
Cost Reduction
By optimizing resources and eliminating inefficiencies, Kaizen allows for a significant reduction in operational costs. Companies can allocate resources more strategically and invest in value-added initiatives.
Companies like Toshiba have succeeded in decreasing their production costs by adopting Kaizen practices while maintaining or even improving the quality of their products.
Employee Engagement and Motivation
Kaizen fosters a work environment where every employee feels valued and involved in the improvement process. This active participation enhances team engagement and motivation, leading to better talent retention and a positive corporate culture.
At Canon, implementing improvement suggestions from employees has not only led to operational improvements but has also reinforced the sense of belonging and individual responsibility within the team.
Flexibility and Adaptability
In a constantly evolving world, the ability to adapt quickly is essential. The Kaizen method, with its iterative approach and culture of continuous improvement, allows companies to remain flexible and responsive to market changes and new opportunities.
Nissan has used Kaizen to adapt to fluctuations in the automotive market, adjusting its production processes in real-time to meet new consumer demands and trends.
In summary, the benefits of Kaizen are multiple and significant, touching various aspects of organizational performance. By adopting this method, companies can not only improve their operations but also create a culture of excellence and proactivity.
To delve further into the advantages of Kaizen, consult this detailed article.
Challenges and Solutions in Kaizen Implementation
Although the Kaizen method offers numerous benefits, its implementation can present challenges that are essential to overcome to ensure its success. Understanding these obstacles and knowing strategies to overcome them is crucial for any organization wishing to adopt this approach.
Resistance to Change
One of the main challenges in implementing Kaizen is resistance to change. Employees may be reluctant to adopt new methods or alter their work habits, fearing the unknown or losing their comfort.
To overcome this resistance, it is important to clearly communicate the benefits of Kaizen and involve employees from the beginning of the process. Training sessions and participatory workshops can help raise awareness and rally teams around the goals of continuous improvement.
Lack of Training and Skills
The success of Kaizen relies on employees’ competence to identify and implement improvements. A lack of adequate training can hinder this process, making it difficult to achieve the set goals.
Investing in specific Kaizen training programs is essential. Practical workshops, mentoring sessions, and educational resources help develop necessary skills and ensure a deep understanding of the tools and techniques of Kaizen.
Maintaining Long-Term Motivation
Maintaining employee motivation in the long term is another major challenge. Without appropriate incentives and continuous recognition, initial enthusiasm can wane, slowing down continuous improvement efforts.
To counteract this, it is important to regularly celebrate successes and recognize individual and collective contributions. Rewards, recognition programs, and opportunities for professional development can help maintain a high level of motivation and engagement.
Integration with Existing Systems
Integrating Kaizen with existing systems and processes can sometimes pose problems, particularly in terms of compatibility and complexity. This can lead to delays and inefficiencies if the integration is not well planned.
For successful integration, it is crucial to proceed in stages, carefully evaluating current systems and identifying points of convergence with Kaizen principles. Collaborating with project management experts and utilizing tracking tools like ProjectManager can facilitate this process.
Time and Resource Management
Implementing Kaizen requires an investment of time and resources, which can be an obstacle for companies already under pressure. Finding the right balance between daily activities and continuous improvement initiatives is essential.
Rigorous planning and the allocation of specific resources to Kaizen projects can help manage this challenge. By setting clear priorities and integrating Kaizen initiatives into the company’s strategic objectives, effective use of time and resources can be ensured.
Despite these challenges, many companies have successfully integrated Kaizen through a strategic approach and a collective willingness to improve. By recognizing potential obstacles and implementing suitable solutions, organizations can fully benefit from the advantages of the Kaizen method.
For more tips on managing challenges related to Kaizen, consult this article.
Additional Resources and Further Learning
For those looking to deepen their knowledge of the Kaizen method and explore advanced application strategies, numerous resources are available. These complementary tools can help refine your approach and maximize the benefits of continuous improvement.
Books and Publications
Books such as Kaizen: The Key to Japan’s Competitive Success by Masaaki Imai offer an in-depth understanding of the principles and applications of Kaizen. These books are essential for anyone wishing to master this method and apply it effectively in their organization.
Online Training and Certifications
Many platforms offer online courses and certifications dedicated to Kaizen. These trainings help develop practical skills and provide official recognition of your expertise in continuous improvement.
For example, training modules are available on specialized sites like Fabriq.tech, offering interactive content and real case studies.
Digital Tools and Software
The use of project management software, such as ProjectManager, facilitates the tracking and implementation of Kaizen initiatives. These tools offer advanced features such as kanban boards, real-time dashboards, and collaborative feedback systems.
These digital solutions allow for more effective management of improvement projects, thus ensuring better coordination and increased visibility on the progress made.
Communities and Professional Networks
Joining communities and professional networks dedicated to Kaizen can provide valuable support and opportunities for experience sharing. Participating in forums, LinkedIn groups, or specialized events allows you to stay informed about the latest trends and benefit from expert advice.
Organizations like Lean Enterprise Institute offer resources and regular events for professionals interested in Kaizen and continuous improvement.
Case Studies and Research Articles
Reading case studies and research articles allows you to understand how other companies have successfully implemented Kaizen and what results they have achieved. These documents provide valuable insights and practical lessons that can be adapted to your own organizational context.
Recent publications, available via sites like WeProc.com, provide detailed analyses and concrete examples of the application of Kaizen across various sectors.
By exploring these additional resources, you can deepen your understanding of Kaizen and discover new methods for optimizing your processes and stimulating innovation within your organization.
#>